Now that the printer construction is wrapping up, I am deep in to testing the scripts, calibrations, and such to enable dual extruder printing. With IDEX setups, (dual independent extruders) calibration is much more difficult than standard “shared” single X gantry extruders where the nozzles are known distances and such from themselves. IDEX printers rely on very accurate end stops to ensure the X axis is aligned. I used hall (Magnetic sensing) end stops for this since they don’t age, and should remain consistent for the long haul.
So far the calibrations have been pretty on point, with only sub .1mm tweaks I am making here and there to tighten things up.
Learning how Simplify3D works with the IDEX printing and such is also a challenge. I am still working on that but i got it to generate functional code for this test print. I am using the Ooze shield option because I don’t have a “wiper” for the extruders designed yet, so the ooze shield catches the pre-extrusion ooze that tends to happen from the stand by extruder before it starts printing.
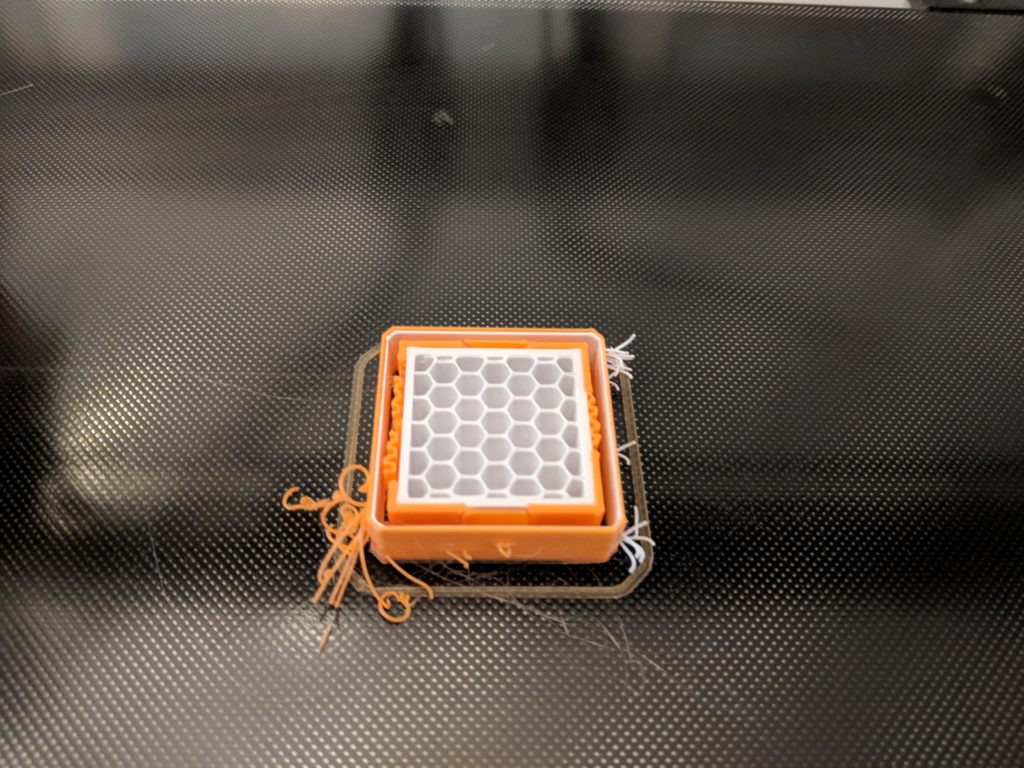
My test print is a 2 color cube I designed for card games that will let you flip up the cube to show what suit is trump for some games. Seemed like an easy, and fast test. This was with an inset second color, next test will be a model with flush muti colored perimeters.
I still have some tuning to do around this but the result was good in the end:
Finished part, not perfect, but not bad either. Ooze shield earning its worth!
Nozzle wiper –
One of the things I’ve been wanting to design on this printer is a nozzle wiper. This is difficult wiht the printer given some of the geometries. Either I build a wiper on each side that stays stationary on the frame and makes the heads come to it, or I design one that attaches to each end of the X Gantry so any time the heads park they get wiped going in and coming out.
The issue is that the heads are a good 100mm or so away from the sides of the printer, 60mm from the stepper, and clearances on the stepper motors to the frame is tight. Another downside is I need to add in extra movement to ensure the nozzle goes to the wiper every time the tool gets called. That seems cumbersome. So I was thinking of a clamp that goes on the stepper and has a small arm that goes down and out to hold a small silicone wiper. It doesn’t need to be strong but it needs to be light to not impart any more mass onto the moving structure or unwanted vibrations. NylonX is perfect for this. Then anytime the end parks, it gets wiped with no additional coding or movements.
So adding this to my to-do list, along with a camera and lighting mounts in the printer.
Next steps – Soluble supports and breakaway supports.
I need to find the right printing setup for both those materials, but that is the ultimate goal here, is to be able to print effectively with soluble supports so I can print pieces in their strongest direction without cares about overhangs. PVA soluble support material is crazy expensive, more expensive than CF Nylon! So I will need to see how this all goes.
I do not want to print with HIPS, one of my overall goals is not printing with anything styrene based (ABS, ASA, HIPS) because 1. the toxic fumes, 2. the toxic waste produced by dissolving HIPS, 3. the toxic materials needed to dissolve the HIPS in general. I may end up working with ASA down the road if I need materials or parts with strong strength and temp resilience and great UV resistance. And I am building an enclosure specifically for materials that need heated/controlled chamber temps + fume off gassing.
Leave a Reply