Over the last few weeks I’ve been doing a lot of work to not only get my workflows down solid for eventually ramping up JK3D.us as a side business, but also expanding my knowledge and capabilities in the world of additive manufacturing. This is a run down of the hodgepodge of projects I’ve been working on.
MSLA Printing with Elegoo Mars 2 Pro
I’ve been very interested in SLA/MSLA/LCD/DLP resin printing for years, well before I was interested in FDM (Printing with filament and melting the plastic together) printing that I normally do. With the launch of the Form 1 SLA printer back years ago the qualities and capabilities of the hyper fine resolution and fidelity of UV cured resin printing was amazing.
Over the years the price point has dropped on these from thousands to hundreds with qualities that rival or even beat in some cases what the Form 1 printers could do. (Form 3 are in a different league these days, but cost 10-15x what this Mars 2 Pro does). There is no FDM printer that can even get close to the detail, layer heights, omnidirectional part strength. FDM can do things MSLA cant as well, multi material prints, stronger materials, larger objects, outdoor stable materials, and speed. So they all have their place.
The technology, processing, designing, printing, post processing, and safety tasks for resin printing are 100% different from FDM printing.
FDM vs SLA/MSLA from a safety perspective.
FDM Printers:
- Fire Risk (Many hot elements in the system)
- High voltage used (110v for heated bed)
- Many parts in motion, risk of damage to the printer and you if you get in the way
- Certain filaments require proper ventilation to avoid bad off gassing (I don’t print with these in most cases)
- Microparticles generated by FDM printing can be hazardous
SLA/MSLA printers:
- Resin is highly toxic in its vapors and if you get it on your skin.
- High intensity UV lighting dangerous to eyes, skin, etc… (Both for printing and curing)
- Cleaning prints requires flammable/toxic chemicals (99% Isopropyl Alcohol in my case)
- Waste products are toxic and need to be handled like Hazmat unless cured
In short… one will potentially burn you and your house down and the other will poison you and everyone around you. Hobbies are fun!
Getting everything setup
To make the cleaning and curing process easier I also ordered a Elegoo Mercury Plus cleaning and curing station. It holds a tank of Isopropyl Alcohol (IPA) for cleaning, a magnetic stir plate, and an array of 2 wave length UV LEDs for final curing of the parts.
The printer/cleaner are up in a utility closet on my roof where there is some ventilation. It sits between my furnace and my K40 laser cutter. The laser cutter is up there for similar reasons that it is away from the rest of the house and can vent easily.
I did some hacking on the printer right away to make it network connected. I am so used to my Duet based printer, that I wanted this one on the network. I used this write up on how to use a Raspberry Pi to control the printer and upload files remotely. It works well, but there are some clear code issues/quirks to it. The Pi sits in place of the USB stick, and then controls the printer via the serial link(the 3 wires going to the GPIO pinouts). I modified a Pi Zero W case to cover the SD and more of the pins so that resin wouldn’t drip in and i didn’t accidentally short the pins. The Pi needs to be outside the printer due to the WiFi setup. Eventually I may go to a NanoDLP controller to replace the stock one.
First prints
Over a few days I played around a bit with the printer but these are my first prints. The Rook is a stock part that comes ready to print from Elegoo, I printed it with some Elegoo ABS-Like resin, which is surprisingly strong and durable, but also stinky.
Next up I wanted to test something complex with supports, and hollowing it with the Chitubox slicer. So I picked something topical. A high res SARS-CoV-2 virus. I played with punching holes in the model, hollowing it, and such to ensure I could get the resin out of the middle.
When working on all this I wear PPE as if I am working with spray paint, I wear a proper VOC respirator, and 7mil nitrile gloves. You are never supposed to touch resin with your fingers unless its been fully UV cured. The pic above of me is from the camera I use to monitor the printer.
Next Steps
Next up I have a few new resins coming in (MatterHackers Build series in various colors, and Siraya Tech Sculpt high temp resin) that I am looking to test. I am specifically going to test printing some parts of my main 3D printer in the high temp Sculpt resin to see how it would perform. I am very excited to have this capability to work with such high detail and resolution printed items, this is a whole different beast than my normal printer. But FDM is still better for many many things than resin printing.
JK3D.us – it’s a thing now
Over the last month (or actually… since almost 12 months ago) I’ve been pondering making a move into offering my skills, and tooling to do 3D printing for others. I have a lot of original designs and capabilities to design items for individuals and businesses, and I might as well leverage it!
The site is online and live, and ready to take orders, but there is still a lot of work I am trying to get done on the back end regarding the business side of things, getting filaments and materials socked up, and getting some small inventory runs done. Currently I have a few parts up on the site that I’ve sold in the past to people before I had JK3D online (via word of mouth).
I am excited at the next steps over this spring to really start pushing this and seeing what I can do with it. I have a dozen or more products ready to get on the site to list for sale but a bit more work to do on my side before that happens. Everything on there can be ordered now though and will ship ASAP.
I am working on other parts and have technically done my first “contract” design and build:
A friend needed risers for his new Yakima rack on his Chevy Colorado so that his tonneau cover can roll up while the racks are on. The factory options are big metal racks that interfere with a cover. I designed these to be super robust printed from CF-Nylon PA6, the walls are close to 4mm thick and there are 2 6x95mm bolts that run to the rail system. He is currently using them and testing them out, if there are no issues I plan to take this design and iterate the design for different heights and list it on JK3D.us.
The design process was quick, I took photos of the landing pads for the rack, sizing of all the rack dimensions/rail dimensions and actually did the nose curve design from the photos I took and it worked out perfectly.
This was one of the first prints I’ve done designing and printing for pure strength and durability, and I think these are now stronger than the rails on the truck – there is 600gm of CF-Nylon (which is already a very light filament) in all 4.
More FDM Printer Maintenance and Repairs
One of the tasks that came up when doing a lot of printing lately was play evolving in the Z table screws. These are the Acme screws on either side of the Z table that move the table up and down. The entire weight of the table rides on 2 Delrin nuts that are secured to the table.
These nuts are some of the oldest wear items on the printer at this point and over time the Delrin does wear and I noticed a good bit of play developing. I purchased backup and replacement ones last year but never put them in. Well the time came. I came up with an easy solution to lock the Z table in place with 4x extra corner brackets and some twist lock T nuts. This held the table steady as both screw drives were dropped out.
It was a pretty fast repair, but pretty messy from all the old grease on the parts.
Outsourcing printed parts
After getting tired of dealing with some heat issues affecting certain key parts of the FDM printer, I outsourced the printing of the X axis components of my printer by Shapeways. I am having all the Xaxis components printed via HP Multi Jet Fusion PA 12/Glass Bead material. It will be slightly heavier, but should be stronger under load and under high temps than the CF-Nylon I am working with. With trying to get JK3D running, I cannot have this printer break down due to material fatigue or heating issues. They should also have the super neat dark gray Multijet look to them. If these work out well I will be replacing a few other parts of the printer with this material. I would love to print this material myself, but a Multijet Fusion printer is about $200,000+

As mentioned above as well, I am going to be testing some high temp/strength resins for certain parts of the printer as well. The heat deflection temp on the high temp resin I have is 160C which is beyond even the Muiltijet Fusion parts!
Raspberry Pi hacking
Another project I have been starting to dip my toes in is using Raspberry Pi’s for other projects around the house. I already use a few Arduino based ESP8266 devices around for specific tasks, but for some upcoming projects I will need the power of a Raspberry Pi to get them done. A few issues with this plan is I have virtually no experience with Python, dealing with Git repositories, haven’t worked in Linux for a decade, and these projects require specialty knowledge of Bluetooth, Ant+, and other hardware… so… we’ll see if I get anywhere by the end of the summer.
Projects I am looking to do:
- In Progress: Ant+ enable my Water Rower – I want to get power, distance, stroke rate, etc… from my Water Rower onto my Garmin Watch so it goes into the Garmin Connect app. There is a project already out there that is doing good work, but so far it wont give the data I need to the watch or use ErgIQ app. Its coming. I have the hardware already to go for it though and it works to some extent:
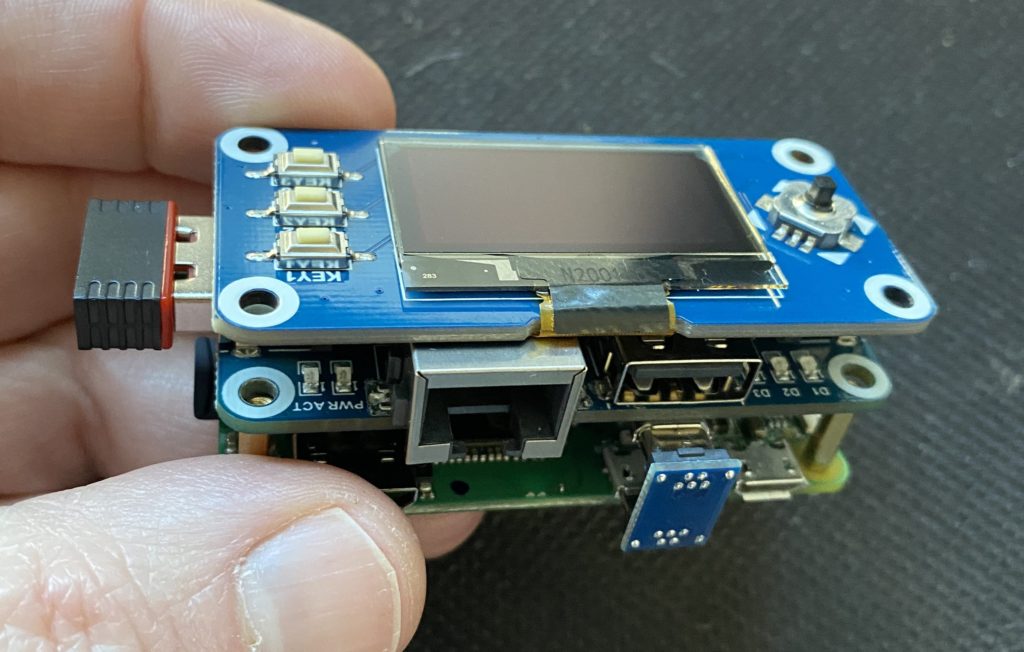
- Not Started: Ant+ Enable and Enable resistance control via BLE for my Sole LCB exercise bike. (noticing a theme here?) The exercise bike we recently picked up has BLE connectivity to apps, phones but has some significant limitations. It wont let apps like Zwift control resistance and wont allow basic workouts to sync to Garmin in any way. The resistance issue is a patent restriction – there is a secured patent that blocks app based resistance adjustment on exercise bikes (trainers aren’t blocked by the patent).
So what I want to do is figure out using a Pi as a “man in the middle” BLE device that will also broadcast the broadcast workout data in the proper Ant+ profile for Garmin/other Ant+ compatible devices to use, and also enable the “Smart Trainer” capability on modern Garmin watches. And wire in the Pi to side step the BLE block the US based bikes have against resistance changes via app (easy enough to have it “click up/down” the resistance button. There is someone who has done similar to unbrick Flywheel bikes a year ago, and I am going to build off of his work as much as I can (the Sole uses an open standards BLE profile it seems not proprietary)- This requires me to pick apart the BLE data stream from the bike and Identify the bits/dataflow/UUIDs etc… so the Pi can interpret the data.
- Figure out the Garmin Smart Trainer / Indoor Bike Ant+ profile data
- Figure out the BLE Fitness Machine Service to control resistance.
- To be clear… I don’t know how to do any of that… yet.
- Completed: Network enable my Elegoo Mars 2 Pro Printer. As seen above, I dipped my toe in the world of Pi stuff with deploying Mariner3D on a Pi Zero W to network enable my new printer.
Leave a Reply