Now that the 3D printer project is wrapped, I am onto designing parts, and upgrades for my K40 laser cutter/engraver (as well as some other design projects for other hobbies). Over the last few weeks I’ve been planning and doing small upgrades and prints for it, and now its all coming around to being ready to rock.
A link to the exact K40 I ordered is here (note, it seems the K40 listed has changed and now does not have the analog power gauge anymore). Based on tips from a friend who was way ahead of me on the K40 journey I picked up a K40 that has an analog power gauge and potentiometer to control the laser tube. This gives you more fine control and enables use of max power on the tube.
I am using the stock cooling tubes, and water pump. I have a 5 gallon bucket with a cover I am using to hold the coolant, and use distilled water + some additives . Other than that and some high voltage silicone sealant for the laser connections, everything else that was included with the K40 got thrown out (the CD, dongle, cheap exhaust tubing, etc…)
Upgraded Exhaust
To take this K40 from the rather questionable product stock, into a machine I want to use long term I had to make some key changes.
Exhaust mitigation is a key factor for a laser cutter. Virtually anything you cut or engrave is going to release toxic or not pleasant gasses/fumes. My K40 is a newer one that has a 120mm AC fan in the back of it built in, older models rely on an in-line fan in the duct. This makes it a little easier to duct the air out but I didn’t find any ducts available on Thingiverse for my use-case.
So I designed my own 90Deg vertical exhaust duct, and 4″ duct hangers for the ceiling. I also downloaded and printed a replacement vent for inside the K40 to give a bigger print area (you can see the difference in some pics lower in this post). I also added an air-assist nozzle to keep smoke from fogging up the beam path and optics.
Exhaust path
One of the bigger issues with a cheap laser cutter is the management of toxic off gassing/fumes/smoke is not handled well at all… so before I even fired up the cutter I made it a priority to build a good fume extraction system/method. I did have the requirement that I am not able to put another 6″ hole through the wall for a vent outside, so I had to become a bit creative.
First was getting the exhaust out of the machine, to do that as the pic above shows I made a nice 2 part 90Deg 4″ duct. I have posted this to Thingiverse for people to download. I attached hangers to the ceiling and put in a 190CFM inline blower down stream to push the air out of the long duct. A video of the exhaust path is below:
Most of the exhaust gasses stay out of the room even with the door cracked open to let the hose out… not as many as I would like, but it does largely depend on the winds.
The top bracket for the exhaust duct is something I am pretty proud of:
The top ledge of our roof has a steel flashing, so I designed a loop that would clamp down on a 4″ duct + an insert (reused the insert I designed for the 90Deg duct on the back of the K40). I put 8 10x3mm magnets I had sitting around from past projects in, and then capped the channels for them. It snaps onto the flashing well and is relatively easy to remove with the pole I have. I haven’t posted this design to Thingiverse since I didn’t know if it would be useful to anyone but me, but I may in the future.
The duct is only out when I am actively using the cutter, and I am going to put an angle at the top to keep any rain out if it happens to start raining during a project.
Air Assist Nozzle
One of the key points I read about on a number of the K40 specific websites as Air Assist/Smoke Assist Nozzles. Some direct the air into the nozzle itself by the mirror, others shoot it in from the side. Due to many reasons having the air blow across the surface is more effective in keeping the material from getting too marred by the exhaust, and also keeps the optics clean.
I went with a 793 GPH Aquarium air pump that sits behind the bucket of coolant I use to cool the CO2 laser. It’s pretty quiet once hooked up. This pump generates a nice strong positive flow of air down a small 1/4″ hose to the head of the laser optics.
I used an extra 8mm drag chain I bought back last year for the 3D printer project but never used. It was perfect size for the hose + the potential wires to install a red dot laser on the end. I modified a design off Thingiverse a mount to use this drag chain and give the clearance I needed.
The nozzle itself is also off Thingiverse and was lightly modified for the hose I am using. There are many designs around this, I liked the direction this one moves the air and its general size the best.
You can see in the above video how effective the nozzle is at moving the smoke away from the optics. I re-printed this nozzle in CF Nylon to give it more heat resistance as the area it is next to can get very warm if burning wood and other high combustion materials.
With the air assist, the effective exhaust ducting the K40 emits little in the way of fumes. I did seal up a bunch of the seams to the laser chamber, and the laser exit hole between the 1st and second mirror I covered in some painters tape and let the laser burn a hole through it. This keeps smoke/vapor/oils from getting in the laser chamber as much and also removes a big area for smoke to get out through.
Cutting Table / Z Axis
One of the big limitations of this laser cutter/end is the lack of ability to alter the focus to any extent. The lens that ships with most current K40’s has a focal point of 50.8mm from the surface of the lens. The table included with the K40 is about 55mm or so from the lens. So its close stock, but you cant adjust if you use anything thick or too thin.
The stock table is a flat sheet of aluminum that has a center section that is only about 120mmx 200mm or so in size that can be removed to expose a spring loaded clamp that is 10+ mm too low for focus.
The For Sale ad Showing the top plate and the clamp under the plate. The K40 I received, and you can see my 3D printed exhaust duct. Cutting table I ordered at the same time as the K40
I ordered a 320×220 cutting table for the laser cutter that will be better in most ways than the stock table. But there is no way by default to mount it or use it while adjusting the height.
I researched designs on Thingiverse, and other premade alternatives and decided I could design something that would use the 320×220 table, could be almost entirely 3D printed, use hardware I already have on hand and re-use as much of the K40 stock top plate as possible. The design will give 40mm of adjustability, with a shallower focus lens and longer screws it would be 50+mm.
The entire setup is on a linked jack screw configuration, so turning any bolt head turns the other 4 at the same time, making adjusting the height super fast and consistent. Check the Thingiverse link below for more build info.
I have posted the design on Thingiverse with a full build of material (BOM), and build notes/instructions. As you can see from the Before/After photo the usable cutting area is now MUCH bigger than it was before. You can also see my craptastic cutting job of the aluminum plate. I used the wrong tool and was in a rush. But in the end it doesn’t matter for the functionality. The build plate does need about 25 mm trimmed off the laser side of the cutter to clear a few metal lips.
The brackets that hold the cutting table leave room to remove the cutting table and drop in a rotary assembly at some point. In the thingiverse link above is a detailed build description and process. This was a weekend build as I had most of the items already on hand to build it other than the 75mm bolts, and a few pullies.
In the end I think the total investment for me in this table was ~$30, but that is because I had all the material and hardware on hand already.
Actually Using the machine
Now with all these changes being made, I have spent my nights working on K40 Whisperer, Inkscape, Photoshop and learning the ins and outs of SVG files, and vector graphics. Part of my first tests was to use a new logo/design for my other website I am working on getting up and online – JK3d.us.
I took the PNG of the logo, threw it into Photoshop and build some vector shapes and colored them properly for K40 whisperer to engrave/cut. You can see in the previously linked video the design being cut.
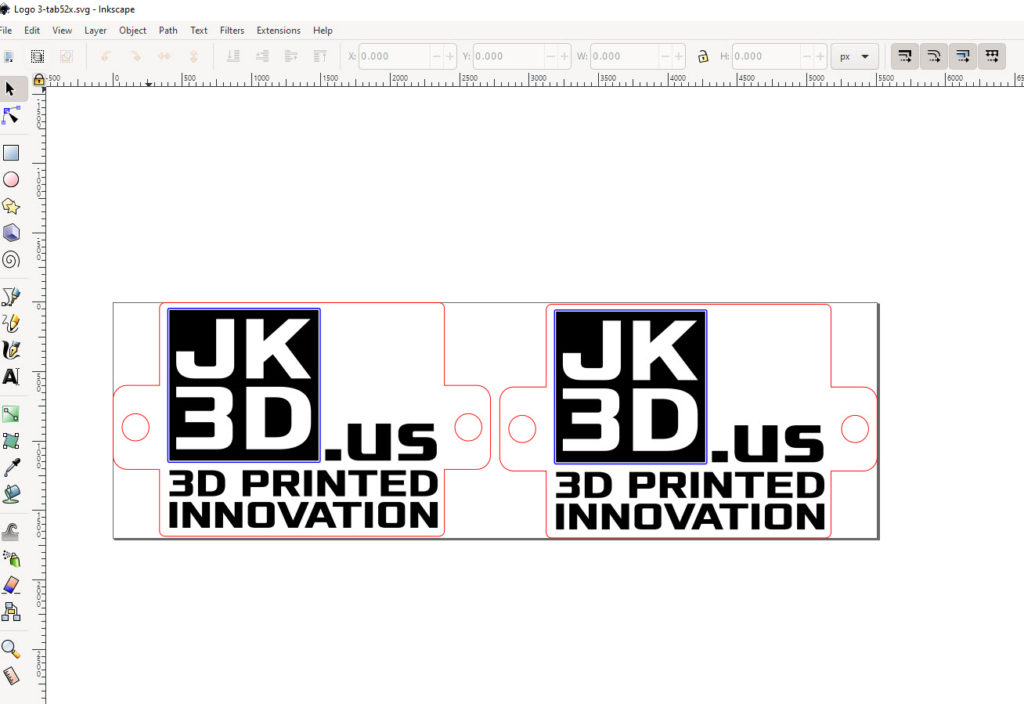
I have a couple sheets of leftover 4mm thick acrylic that I have been using to do these tests. I need to order more material to test other processes. I am starting to build my material specs/list to keep track of power levels and speeds. K40 Whisperer is basic, but incredibly functional for a free bit of driver software for the K40.
And now for another video of the cutting process of the JK3d.us logos:
JK3D.us: It’s happening
As you can probably determine from the videos and pics, I have a new project happening. I am pushing forward since I have time in the pandemic to start my side 3D printing/product business. I am starting this as a site to sell specialty wares I already have designed and make for various hobbies I am involved in (Backpacking, Photography, Motorcycling, Random home improvement tools, etc… ).
Eventually I may actually list a full 3D printer kit as a product as I have all the designs for an incredibly high end printer, and I think I can get it down to a reasonable price for a DIY Kit.
The website is not online yet and I am in the beginning phases of getting it setup at this point, but it is the next big thing I am working on now. I still don’t know the depth/scope of what I am looking to do… but I am feeling pretty passionate about this industry and hobby and I believe I have a lot to offer people getting into it!
Leave a Reply