
With orders rolling in for gear for the new printer every day, testing has started with some of the electronics, and parts that have come in to further validate some design decisions being made in CAD design still. I did run into some issues with the main controller ethernet board… it locks up after a reset. I have some pings into Duet3D already to see if this is a known issue.
One of the key items that had to be tested and documented was the hall sensors used for the end stops. These are cheap sensors, so there is going to be some variance and differences in tolerances.

Coding:
Starting to dig into the coding and config of RepRap firmware on the Duet2. The language and process is completely different from the Marlin firmware I’ve worked on before.
Already getting the basics in for the 8 stepper motor configs and the basic specs. The complicated bits will come in to configure tool changing, and macro scripts. All the code can be done in the web page on the controller itself.
Too Heavy:
One thing that came up that has me a bit concerned is the weight of the build plate I have.
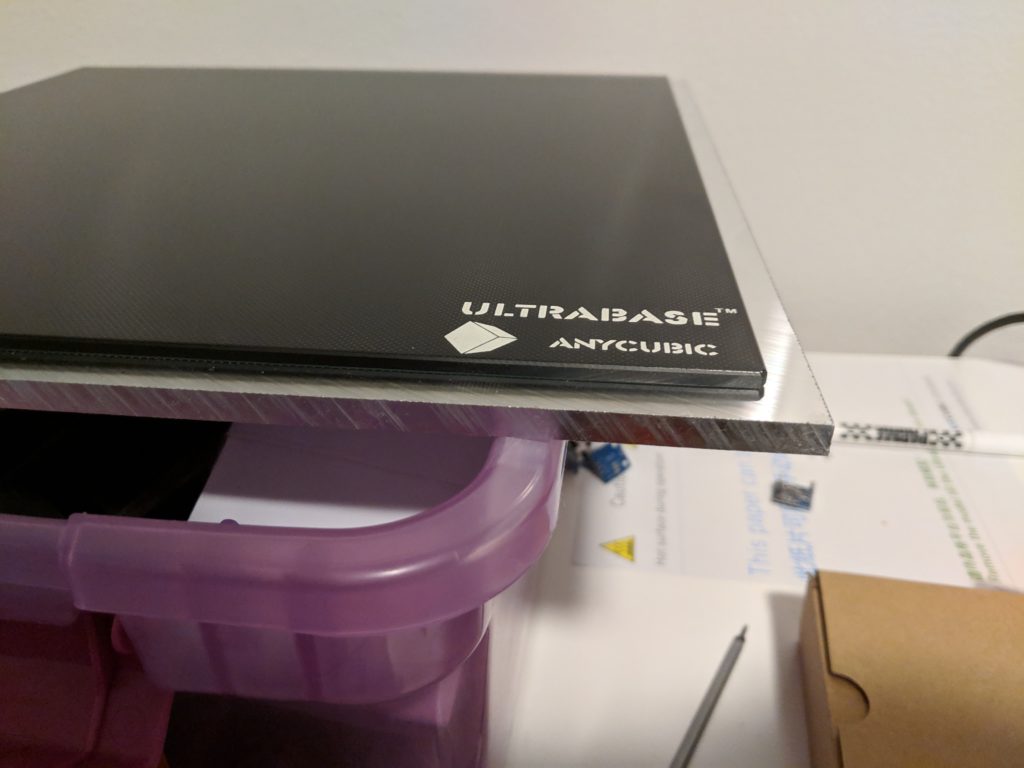
The build plate + Borosilicate plate on top of it weighs close to 7#. This is a lot for the Z motors to handle as well as the materials to support it. I have some options to get some 3-4mm build plates that could be lighter, but they wont be available for a few weeks. This build plate may be something I keep around if I end up using higher power heaters in the future. I need to get it worked on by a metal shop around here with a CNC at some point (to groove a thermistor path, and corner mounting holes.) as well.
Dealing with China…
I ordered some cheap linear rails from AliExpress… $150 vs $460 for legit HiWin rails. After I placed the order I had instant second thoughts, and canceled it a couple days later (It takes like 2 weeks for order to process on that site). I never received an actual confirmation of the cancelation, but no updates happened for another 9 days. I ordered legit HiWin rails and blocks because the motion system is the most critical part of the machine… I don’t want to deal with knock off shit.
Then today I get an email that cancelation was rejected and they shipped… 9 days after the cancelation. So now I have an extra set of chinese linear knock off rails.
Materials:
I ordered the roll of the material all the structural and mechanical parts will be printed out of. 3DXTech CarbonX Nylon. https://www.3dxtech.com/carbonx-carbon-fiber-nylon-gen-3-3d-printing-filament/
This material is crazy rigid, generally high temp tolerant, and has a nice matte black look.
For non structural bits, I am printing in Hatchbox Opaque Orange PETG. Which is a normal filament that is still very strong and temperature tolerant. PLA cant be used in a printer like this that will be enclosed due to low melt temps.
I also will be using Polymaker Polyflex, and eSun eFlex TPU for various parts that needs flexibility to it. One key area I will use these are for wire guides to remove wire stress.
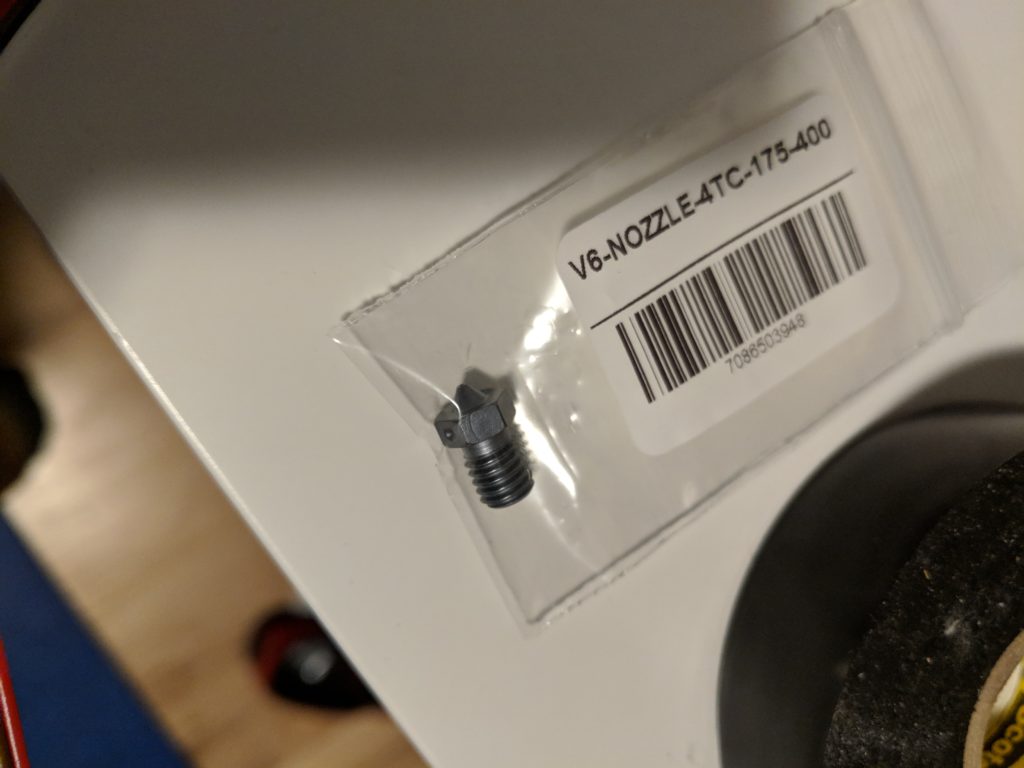
To print everything I will be using 3 different nozzles.
- e3d Brass .40 – This is a standard nozzle that will be for most of the PETG in the printer.
- e3d Brass .25 – This will be used for 2 very small parts (holders for the Hall sensors to keep them aligned and protected). I need more detail than the .4 can handle.
- e3d Hardened Steel NozzleX – This is a brand new specially coated hardened steel nozzle that can handle the carbon fiber loaded filaments I will be using to print the structural parts of the printer. Those filaments will cut through brass like butter if you use those nozzles.
Wire Guides:
Speaking of running wires. I have a few sizes of drag chains/cable chains to use it to guide the wires for the Y and Z axis.

One issue I ran into when testing with them, is while a drag chain like this can be used on the Z Axis just fine, on the high speed Y Axis, I think they would add a ton of vibration and cogging as the links roll over.
So I will be using some nylon wire braiding I have for the Y Axis to give some structure to the wire without the cogging that the chain would have given.
Next Steps:
Waiting on deliveries of the frame materials and linear rails, later next week. I am also waiting for the remainder of the motors, belts and pulleys some of which are being held back ordered for a few weeks.
Once I am confident in my CAD simulations I will start printing some validation prints of the more complex parts.
Leave a Reply