My 3D printing projects have been progressing at a modest rate. The printer itself has moved to a more long term location in my office on the floor which makes working on it kind of PITA, but it prints fine there. I’ve been printing small parts for a few other hobbies lately (like the sprinkler head post a few weeks ago), and working on refining the code for the printer and the Simplify3D profiles.
One big step I made in the last week was while printing some add-on camp chair feet for backpacking I designed, I wanted to get duplication printing working on the printer. This setup uses both print heads at the same time to print the same object twice. This doubles the effective printing speed of the machine and makes doing the same object multiple times pretty easy.


The end results are pretty fun to watch.
There should also be a way to set the other print head to print in a mirror mode as well, but I haven’t setup a “tool” in the Duet firmware to do that yet. Also that carries a bit more risk because the heads could collide in that mode if there isnt an adequate buffer between the print “zones”.
Print Head tweaks:
Because to do this kind of printing both heads need to be at the exact same height, I modified the X-Axis carrier (the one on the left) to have some movement in the 4 mounting holes that the extruder mounts to. This gave it about 1mm of vertical movement so I could set it to match the Right extruders height. From some testing it seems like I am now dead on with the alignment on these. I am going to itterate the actual design of the X Carriages to allow both to have some vertical adjustments for nozzle heights.
I also changed the nozzle on the right extruder to be a matching e3d NozzleX (hardened steel) setup to match the Left extruder. So they can both print carbon fiber loaded filaments now. I’ve not seen any issues printing with steel nozzles with any filaments so far so I am just planning to keep these nozzles as-is unless I need to print something wtih smaller extrusion widths. (these are both .4mm nozzles).
I am unable to tell any quality differences between parts printed with either extruder which makes me pretty happy.
Camp Chair Feet
One of the objects I designed and printed was some wider feet for a Helinox Chair Zero backpacking camp chair. These chairs have small round feet that will sink quickly in to soft soil. Being a heavier person on these little chairs, I wanted to make something to allow the chair to be more stable on soft ground. I designed some feet years ago for a larger Helinox Chair One/REI Flexlite chair and they worked well, but I wanted something a bit more refined for the Chair Zero.
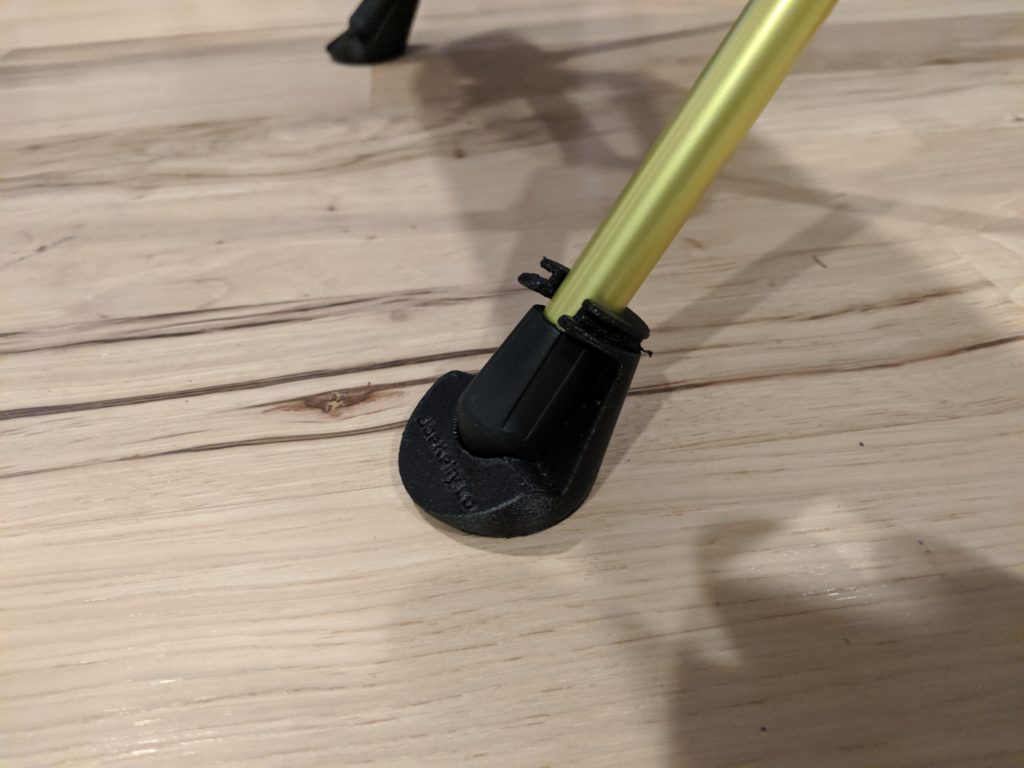
The design is made light and using NylonX material is very durable. It snaps on securely and can be further secured with a zip tie if someone wanted. Each weighs only 10gm, so just about 1oz total for all 4. I did the math and because I am using very expensive filament, they cost ~ $7 in material for a set. I am going to try printing the same design in PETG for better color options and see if they are strong enough.
The foot profile is angled in a few ways to make the foot stable and ensure it stays on the leg on uneven ground.
I will be posting the feet design to Thingiverse but currently that site is having issues with uploads it seems.
Leave a Reply